In the ever-evolving landscape of industrial technology, Manufacturing Execution Systems (MES) have emerged as a cornerstone for modern manufacturing processes. As industries strive for increased efficiency, accuracy, and traceability, the role of MES in integrating and optimizing manufacturing operations has become increasingly vital. This article aims to unpack the intricacies of MES, explore its key features and benefits, and discuss its impact on the future of manufacturing.
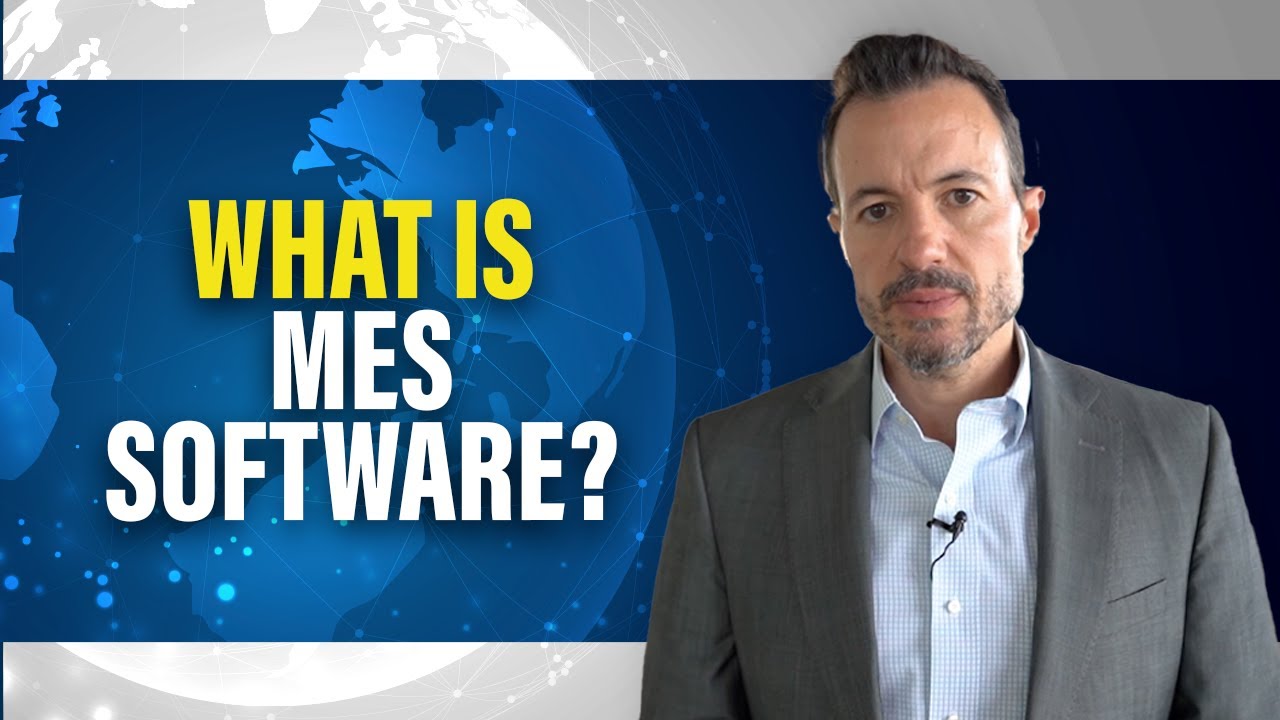
Table of Contents
ToggleUnderstanding MES: The Backbone of Modern Manufacturing
At its core, MES functions as a bridge between the shop floor and the enterprise-level management systems. It tracks and documents the transformation of raw materials to finished goods, providing real-time data and control over the manufacturing processes. This system is designed to improve productivity, enhance quality, and ensure compliance, acting as a central point for managing complex manufacturing operations.
Key Features of MES:
- Real-time Data Collection and Analysis: MES systems gather data from various sources like machines, operators, and quality systems. This data is analyzed to provide insights into the production process, helping in identifying bottlenecks, predicting maintenance needs, and optimizing workflow.
- Process Control: MES allows manufacturers to standardize processes, ensuring consistency and quality. It can control aspects like machine parameters, material flow, and work instructions, aligning the production process with predefined standards.
- Quality Management: Quality checks are integral to MES. It monitors product specifications and controls quality parameters, thereby reducing defects and ensuring compliance with industry standards.
- Performance Analysis: Through Key Performance Indicators (KPIs), MES tracks the efficiency and productivity of the manufacturing process. This helps in identifying areas for improvement and benchmarking against industry standards.
- Inventory Management: MES provides real-time visibility into inventory levels, reducing the likelihood of stockouts or overstock situations. It can synchronize supply with production demand, improving overall inventory turnover.
- Labor Management: It tracks labor productivity and identifies training needs. By aligning workforce capabilities with production requirements, MES optimizes labor utilization.
What exactly is an MES System and what do you need to know about them before selecting the software for your operation? In this episode of our Digital Stratosphere Podcast, we answer those questions and more to help you get the most out of your MES software: What is EMS Software?
Benefits of MES:
By integrating and automating various aspects of the production cycle, MES delivers a multitude of benefits that are essential for manufacturers looking to thrive in today’s complex and fast-paced market. Let’s delve into the key advantages that MES brings to the table:
- Increased Efficiency: MES streamlines production processes, reducing cycle times and increasing throughput.
- Improved Quality: By ensuring processes adhere to specified standards, MES helps in reducing rework and scrap, leading to higher quality products.
- Enhanced Visibility: MES offers a transparent view of the entire manufacturing process, from raw material to finished product, aiding in decision-making and strategy formulation.
- Cost Reduction: Through optimization of resources and processes, MES can significantly lower manufacturing costs.
- Compliance and Traceability: In industries like pharmaceuticals and aerospace, where compliance is critical, MES ensures adherence to regulatory standards and provides detailed traceability of products.
MES Integration with Other Systems:
A key strength of MES lies in its ability to integrate with other systems like Enterprise Resource Planning (ERP) and Supply Chain Management (SCM). This integration enables seamless information flow across different levels of the organization, leading to better coordination and decision-making.

MES in Various Industries:
The application of MES transcends various sectors, from automotive to electronics, pharmaceuticals, and food and beverage. Each industry tailors MES to address specific challenges, such as compliance in pharmaceuticals or complex assembly processes in automotive manufacturing.
The Evolution of MES: From Simple Tracking to Advanced Analytics
Initially, MES systems were primarily focused on tracking and documentation. However, with advancements in technology, their scope has expanded to include advanced analytics, predictive maintenance, and integration with technologies like the Internet of Things (IoT) and Artificial Intelligence (AI).
The Role of IoT and AI in MES:
- IoT: IoT devices provide a wealth of data from the shop floor, which MES uses to monitor processes in real-time, predict equipment failures, and optimize maintenance schedules.
- AI and Machine Learning: AI algorithms analyze vast amounts of data to identify patterns, predict outcomes, and suggest process improvements. Machine learning can also be used for predictive quality control, further enhancing the capabilities of MES.
MES and Industry 4.0:
In the era of Industry 4.0, MES is pivotal in connecting various digital technologies, thereby forming the backbone of a smart factory. It plays a crucial role in achieving digital continuity, from design to production and supply chain management.
Challenges and Considerations in Implementing MES:
As we delve into the transformative potential of Manufacturing Execution Systems (MES) in modern manufacturing, it’s crucial to address the flip side of the coin – the challenges and considerations that come with implementing such a comprehensive system. While the benefits of MES are substantial, navigating the implementation process can be a complex and demanding journey, fraught with potential obstacles and key decisions.
In this section, we will explore the common challenges that businesses often encounter when integrating MES into their operations. From issues of system integration and data security to the hurdles of change management and scalability, understanding these considerations is vital for a successful MES deployment. Let’s unpack these challenges to better prepare for a smooth and effective MES implementation.
- Integration with Existing Systems: Integrating MES with legacy systems can be challenging. It requires a clear strategy and often customization to ensure compatibility and data integrity.
- Data Security: With the increasing reliance on data, ensuring the security and privacy of information collected and processed by MES is paramount.
- Change Management: Implementing MES involves significant changes in processes and workflows. Effective change management strategies are necessary to ensure smooth adoption and utilization.
- Scalability and Flexibility: MES solutions should be scalable to adapt to growing or changing business needs. Flexibility to incorporate new technologies and processes is also essential.
The Future of MES: Trends and Directions
As we venture further into the digital age, the landscape of manufacturing continues to evolve at an unprecedented pace. This evolution brings with it a future rich in potential and innovation for Manufacturing Execution Systems (MES). In this section, we will explore what lies ahead for MES – examining upcoming trends, technological advancements, and the shifting paradigms that will shape the future of these systems.
From the integration of cutting-edge technologies like AI and IoT to the increasing focus on sustainability and cloud-based solutions, the horizon is bustling with exciting possibilities. Understanding these future directions is not just about keeping up with technology; it’s about leveraging these advancements to stay ahead in the competitive and ever-changing world of manufacturing. Let’s take a glimpse into the future of MES and how it is poised to redefine manufacturing efficiency, productivity, and adaptability.
- Cloud-Based MES: The shift towards cloud-based solutions offers flexibility, scalability, and reduced IT overhead. Cloud MES is particularly appealing to small and medium-sized manufacturers.
- Augmented Reality (AR) and Virtual Reality (VR): These technologies are beginning to integrate with MES to enhance training, maintenance, and even remote assistance.
- Sustainability and MES: There’s a growing focus on using MES to track and improve environmental sustainability in manufacturing processes.
- Customization and User-Friendly Interfaces: MES providers are focusing on more user-friendly, customizable interfaces to improve user experience and accessibility.
- Greater Collaboration: MES is expected to foster greater collaboration between different departments, suppliers, and even customers, creating a more integrated and responsive manufacturing ecosystem.
Conclusion
Manufacturing Execution Systems have transformed from simple tracking tools to sophisticated systems that are integral to the digital transformation in manufacturing. By providing real-time data, process control, and analytics, MES enhances efficiency, quality, and compliance. As we move forward, the integration of emerging technologies like AI, IoT, and cloud computing will further expand the capabilities and impact of MES. In an age where agility, efficiency, and innovation are paramount, MES stands as a critical enabler, helping manufacturers navigate the complexities of modern production landscapes and stay competitive in a rapidly changing world.
I would enjoy brainstorming ideas with you if you are looking to strategize for an upcoming transformation or are looking at selecting an ERP system. Please feel free to contact me at eric.kimberling@thirdstage-consulting.com. I am happy to be a sounding board as you continue your digital transformation journey.