Lean Six Sigma became very popular in the 1990s. But, in today’s era of digital transformation, it seems to have been lost in the shuffle. In this blog, I want to talk about why it’s time to bring back Lean Six Sigma for those of you that may have forgotten about it in your digital transformations.
Let’s jump back in time a bit and set the stage…
In the 80s, and 90s and even into the 2000s, Lean Six Sigma was something that became very popular, especially with manufacturing organizations and really any company that was hyper-focused on quality and reducing cost.
Over the years, as we got more enamored by technology, big complex digital transformations, and emerging technologies – Lean Six Sigma became overshadowed. I want to show you why Lean Six Sigma is so important to transformation and why you should consider Lean Six Sigma with your business transformation.
Table of Contents
ToggleOverview of Lean Six Sigma
To begin, it helps to understand what exactly Lean Six Sigma is. Many of you may already be familiar, or maybe you’re a Six Sigma Black Belt. But, for the rest, you may have forgotten what it is, or maybe you’ve never heard of it. Lean Six Sigma in summary is a way to reduce waste, to increase quality. How does this happen? Let’s break it down.
These strategies focus on reducing defects and maximizing customer value within your day-to-day operations. The focus is on value stream mapping, it’s very concentrated on measuring results, and looking for ways to improve results. It’s a way of diagnosing root cause analysis of what is holding back the organization from being more efficient or more effective.
The origins of Lean Six Sigma are traced back to the Japanese auto industry back in the 80s which was made mainstream in America by General Electric and some other organizations like Motorola. This is essentially how Lean Six Sigma became part of the today’s business vernacular. In summary, Lean Six Sigma is a way to improve operations and create a culture of continuous improvement over time.
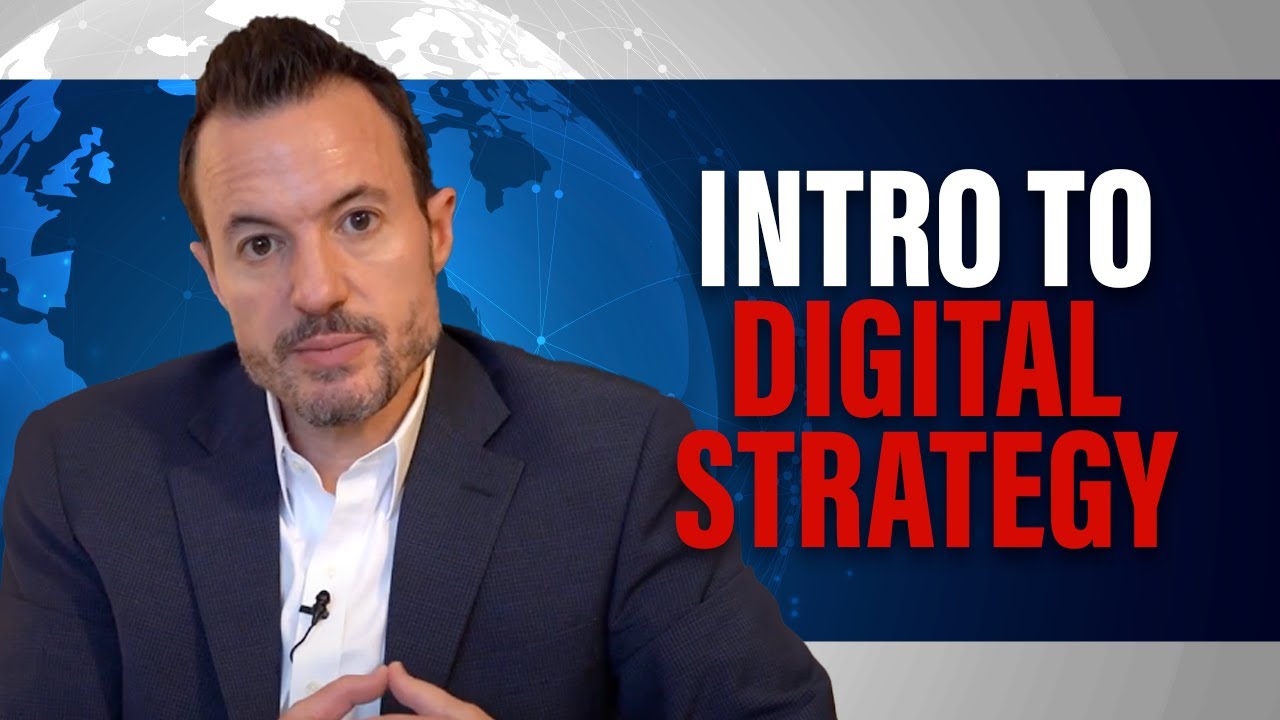
The Drive for Technology and Operational Excellence
If you talk to a software vendor, whether it’s an ERP software vendor or any sort of business technology provider, chances are pretty slim that they’re going to be talking about Lean Six Sigma. Usually, they tend to lead with the technology and talk about all the great bells and whistles that their systems provide.
The beauty of Lean Six Sigma is that it’s very technology agnostic. It doesn’t really matter what sort of technology you’re deploying. The overall idea is more focused on how you can improve your operations instead of any particular technology or software system.
The reason why losing sight of Lean Six Sigma or in your transformation journeys can be a big mistake is because it results in organizations deferring to technology and letting the system drive the way the business is going to be run, rather than focusing on your operations and optimizing your customer value.
A second example of how Lean Six Sigma can drive your technology and really allow the dog to wag the tail rather than the tail wagging the dog, is that by focusing on value stream mapping, optimizing your processes, and defining what you want your processes to be in the future. This gives you a clear set of criteria to evaluate potential technology options. It also provides a foundation to identify where the technology you might be deploying is deficient.
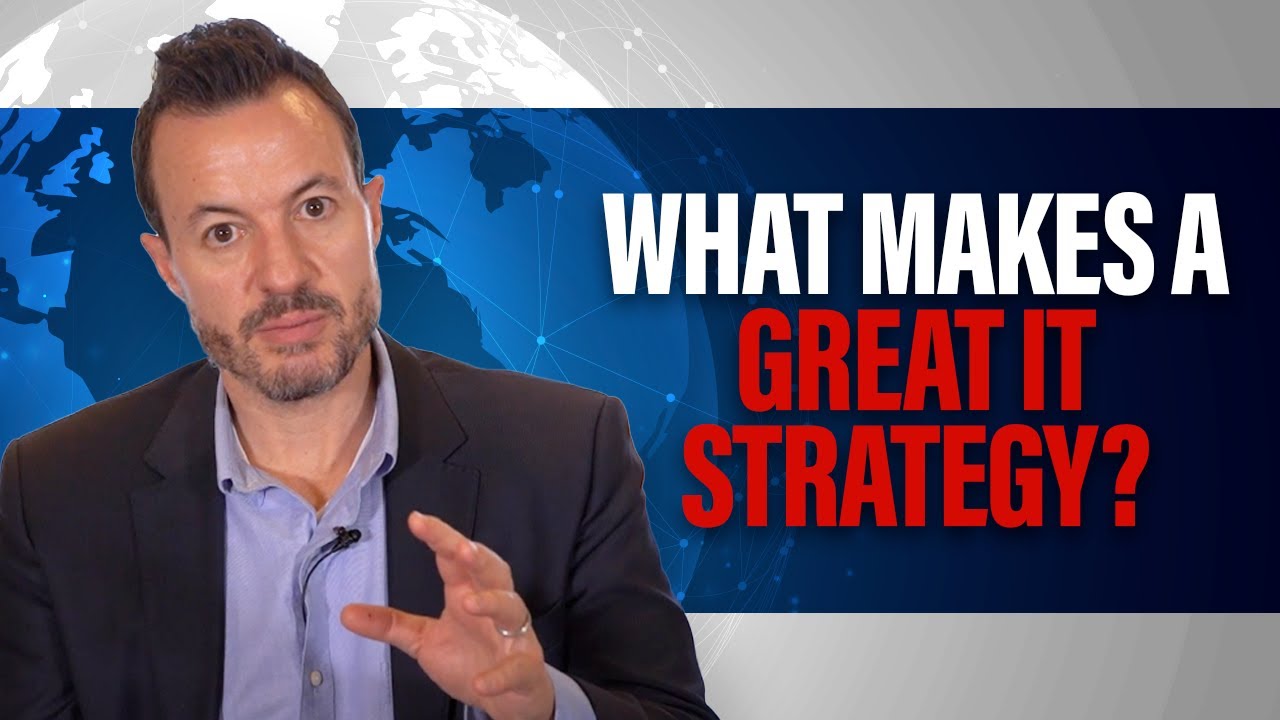
No technology is perfect, and every system you might deploy is going to have deficiencies and weaknesses that need to be addressed. It is important to have that clear vision through value stream mapping within a Lean Six Sigma framework. With these exercises, you’re going to have a much better sense of which technology can best fit your organization, how you can best deploy that technology, and how to fill any gaps.
Focus on the Metrics
Another important benefit of Lean Six Sigma is that it focuses on metrics. It’s a very quantitative-driven framework that is almost obsessed with measuring what’s happening throughout your operations. In fact, Six Sigma focuses so much on analyzing data and identify optimization tactics that it can really benefit any transformation initiative.
These metrics can then be used, not only for your implementation and setting the goals for what you want to get out of your implementation but also from the perspective of continuous improvement post-implementation as well.
Root Cause Analysis
One of the more powerful tools of Lean Six Sigma is a little whole concept of root cause analysis and diagnosing the core reasons why certain problems are happening within your operations. This is an area that not enough organizations dive into when they’re deploying new technology.

This methodology focuses so much on just configuring the existing technology. It works from a data perspective to identify the root causes of why you’re experiencing operation issues or inefficiencies. It can be very beneficial to leverage some of the tools and practices from Six Sigma, to improve the way that you’re managing your overall digital transformation. This goes not only for the implementation itself but also post-implementation as well.
Benefits Realizations and Optimization
One of the biggest challenges with digital transformations is that not enough organizations get the business value or the results that they expected out of their technology investments. The good news with Lean Six Sigma is that it is focused on continuous improvement. The processes are consistently evaluating the value of the technologies, operations, and people/resources to identify any opportunities for efficiencies. The max value or RIO is in the long run. These constant assessments target removing bottlenecks, dropping waste, and reducing defects.
In the end, Lean Six Sigma is built to enhance your operations before, during, and after implementing your new technology. Once you’ve deployed a system to the extent that you haven’t addressed a lot of these abilities, or opportunities to improve your operations, Lean Six Sigma can provide the toolset and the framework to help optimize your benefits longer term.
Ideally, you would move this workstream forward so that, as you’re deploying new technology, you’re maximizing benefits from day one of go-live. Even organizations that do that rarely achieve most or all of the benefits that they expect. It definitely is an ongoing journey of continuous improvement. Optimizing is the best way to ensure that you’re getting the most business value out of your investments in technology.
How to Begin the Journey
With all this being said, the intent of this information is to provide you a quick overview of Lean Six Sigma, and how Lean Six Sigma can help enable a more effective digital transformation.
To learn more, I want to share with you our 2021 digital transformation report. It’s a free download and contains a whole host of best practices for how to deploy new technology, how to manage your digital transformation, and even how to evaluate different sorts of technologies and provide some independent rankings of different software options out there in the marketplace. I encourage you to check this out as well as the rest of our resources found on our website.
I hope you found this information useful and if you have any questions or would like to brainstorm ideas related to your digital transformation, please reach out to me directly. I’m always happy to be an informal sounding board for you and your team.
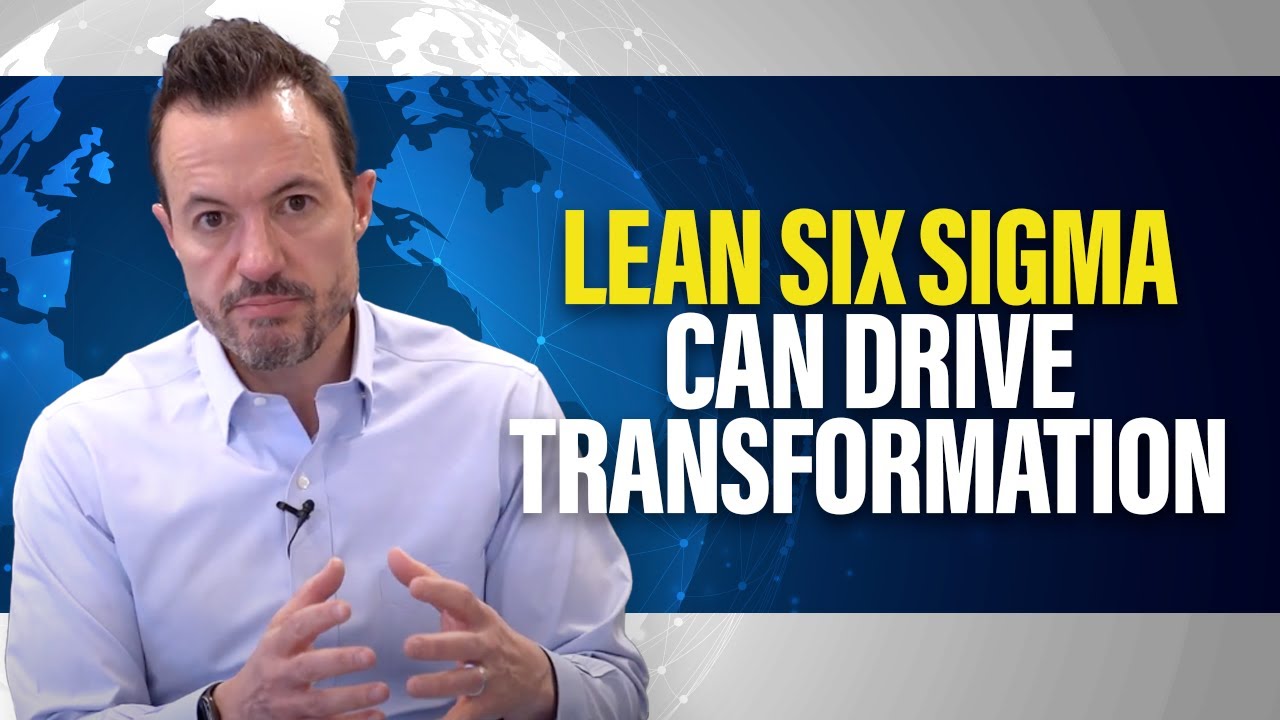