Warehouse management is one of the most critical components of a supply chain. There are plenty of technologies that can help automate the warehouses within any organization, but the big question is how a warehouse management system can potentially automate the entire process.
Table of Contents
ToggleInventory Management
The most fundamental aspect of understanding warehouse management is the concept of inventory management. When thinking about a warehouse or a big distribution center, there are a variety of raw materials and finished goods. There is work in progress stored in those warehouses, so managing inventory and other assets are essential to moving forward.
The cost of the inventory is critical, not only from a price perspective but also, ensuring suitable raw materials and finished products are available. One of the keys to effective warehouse management is keeping track of the inventory, being aware of how much inventory is on hand, knowing its location in the warehouse, and how to get it out the door to customers.
There are a few things to consider when thinking about warehouse management.
- Raw materials– Received into the warehouse.
- Finished goods– Complete product to be shipped to customers when the other processes are complete.
Pick, Pack, and Ship
The next dimension of inventory management to be aware of storage locations. These specific areas within the warehouse are where a raw material or a finished good is stored. The main reason this step is so important; when receiving an order, the next step is to fill the order. The warehouse management software will typically show where that inventory is, allowing the crew to easily find and prepare for shipment.
A critical process or function within warehouse management is the entire pick, pack, and ship process. This is when the process of pulling whatever material is needed so that it is ready to ship out to the end customer and shop floor. When shipping to the end customer, there is a process.
- Fill
- Scan the barcodes
- Print the labels
- Place the packing materials
- Ship the product
This is where technology and software can help automate some of these processes. Think about these massive distribution warehouses with multiple storage locations, docking stations, and trucks that can pick up spots. There is a lot to manage. Software and technology can help automate the process to stay on track of inventory throughout the pick, pack, and ship process.
Another consideration, in addition to warehouse systems, is the concept of robotics. Leveraging this emerging technology to retrieve products and materials from the warehouse storage location. A robot will pull the product off the shelf, put it on a conveyor belt, and send it to where it needs to go.
These are just a couple of examples of how technologies can help automate that pick, pack, and ship process. Regardless of what technology is being used, both are essential pieces of warehouse management strategies.

Physical Inventory & Cycle Counts
Even with the best technologies and keeping track of inventory levels, human behavior and interaction with the systems can often result in those inventory levels getting misaligned.
There is also theft which depending on the industry, might have high-value items that walk out the door with some employees. This causes a discrepancy in the system. Most warehouses manage this process and ensure that they keep the system coordinated with some of these human errors that contribute to the inaccuracies due to cycle counts and physical inventories.
Physical inventories are a detailed count of every product within the warehouse. It is extremely time-consuming and typically shuts the warehouse down where all hands-on deck is needed to count everything. Most warehouses go through this on an annual basis.
In between these annual physical inventories, there are also cycle counts, and this data capture could take anywhere between four to an eight-week duration. They are usually high-value items that are more likely to have discrepancies. Physical inventories and cycle counts are two central processes that help ensure that the inventory levels within a warehouse stay coordinated.
Inventory Optimization
A crucial part of warehouse management is ensuring that you have the correct inventory levels. In the past, organizations would often focus on keeping a “just-in-time” inventory level. This is meant to reduce the dollars sitting in the warehouse by having too much inventory. Ideally, this strategy is key to ensuring the merchandise gets out the door right when it is needed.
However, with the pandemic and supply chain disruptions that organizations see more recently in the 2020s, that is becoming less of a priority. Organizations are stocking up on inventory in a way they have not in years past. Whatever the goals and objectives are, there needs to be a clear and deliberate strategy for managing these levels and finding the right optimal level of inventory. There might be different techniques and tactics for several types of merchandise.
If it is high-volume stuff or overly critical components that will disrupt the entire production supply chain. In this scenario, it might be best to keep more inventory on hand. On the other hand, if it is a slower-moving product that you rarely use, there might be a lower inventory level because there is a risk of running out, and if that happens, it’s not going to be a huge deal.
In the end, it is key to make sure the proper inventory optimization is available. The use of warehouse management software to automate and optimize those inventory levels depending on the goals and objectives that are set within the organization.
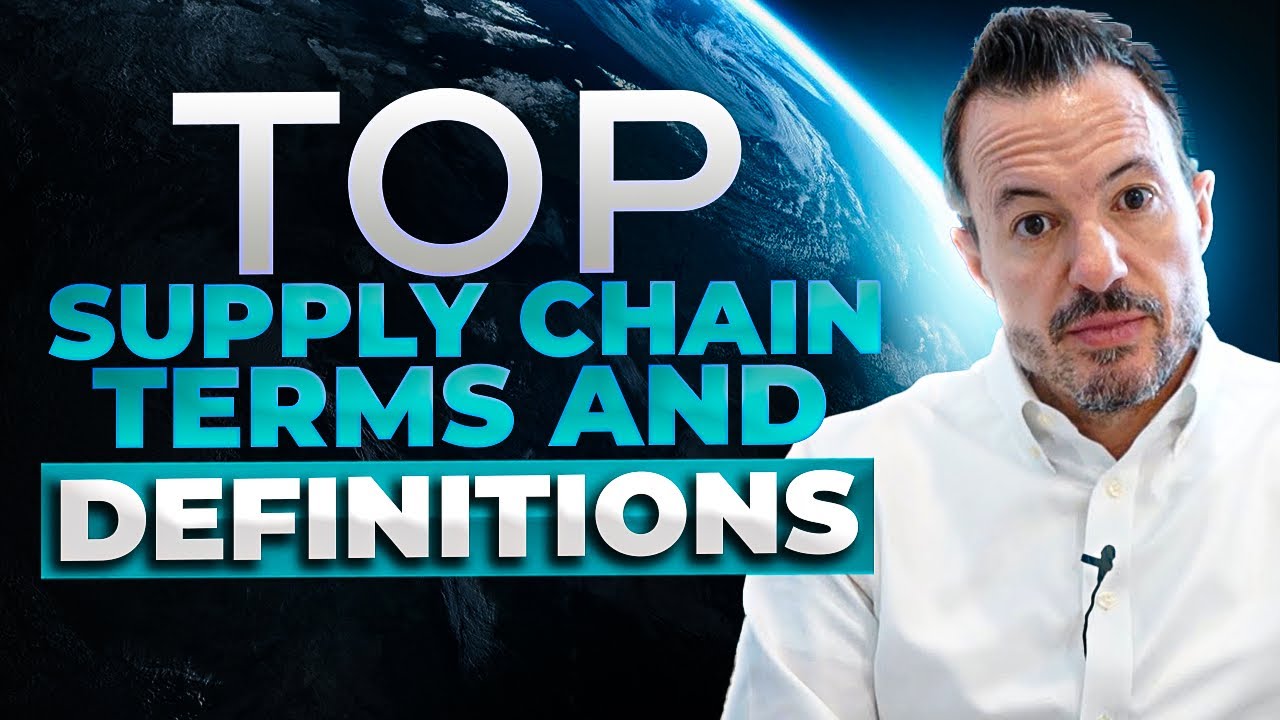
WMS Technologies
There is a concept called warehouse management systems. A WMS can automate the processes, tie together data, and the workflows that connect within the warehouse. There are three different layers of technologies that are needed to leverage WMS.
Layer 1: A focused, best-of-breed warehouse management system. These would be technologies such as HighJump, JDA, or Blue Yonder.
Layer 2: Supply chain management. Vendors like Manhattan Associates, provide complete, comprehensive supply chain technologies that handle warehouse management, procurement, freight logistics, and transportation management.
Layer 3: Broader enterprise-wide ERP systems. These are enterprise resource planning technologies that do warehouse management, supply chain, financials, general inventory management, accounting, CRM/ sales, human capital management, and HR.
Remember, there are a plethora of technologies to choose from depending on what kind of strategy fits the roadmap of the organization. It is not a one size fits all approach and therefore, it is important to do perform some due diligence before using them.
Resources
For more information about these vendors, I encourage you to look at some of the top ten rankings of WMS, supply chain management, and top ten rankings of ERP vendors all featured in the 2021 Digital Transformation Report. This report provides best practices for warehouse management and much more.
If you have any questions regarding these systems or warehouse management in general, please don’t hesitate to reach out to me directly. I am happy to be an informal sounding board as you move through your digital transformation journey.
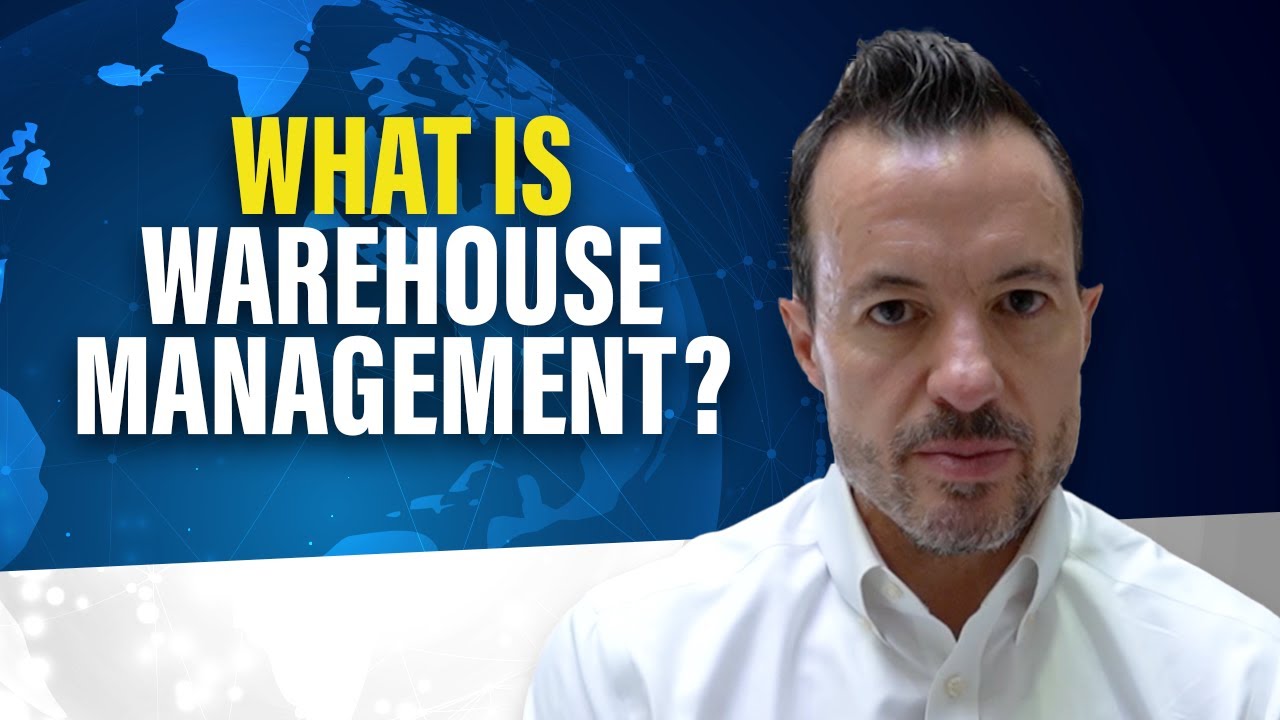