Is the Value of As-Is Mapping Worth the Pain it Takes to Create?
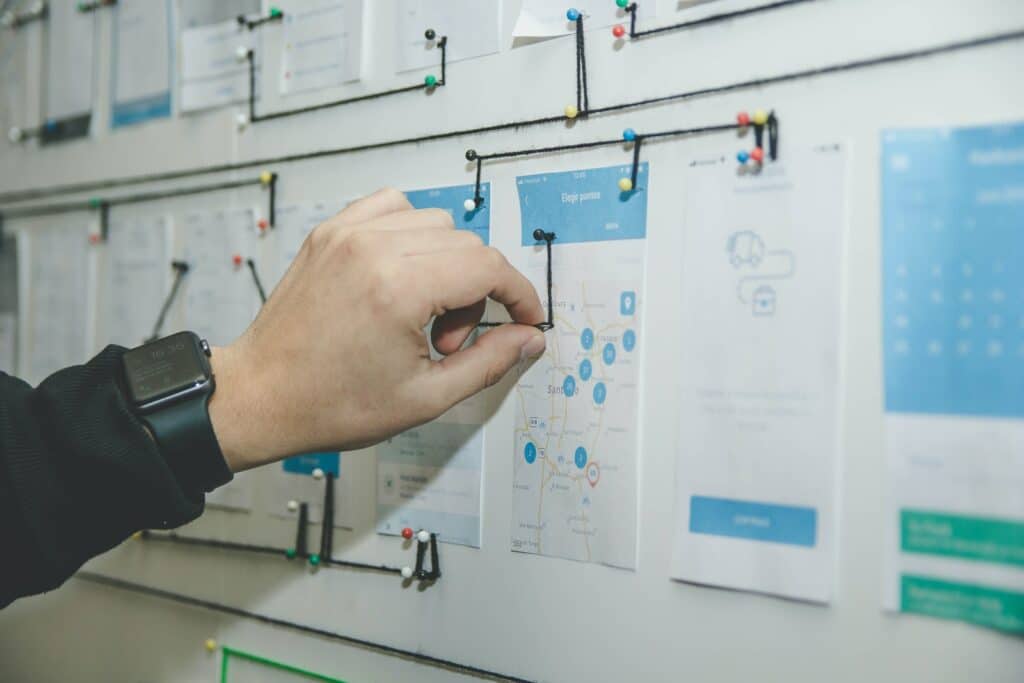
Although there is an almost unanimous consensus that mapping business processes for the to-be state is an important step in preparing for an ERP implementation, the same cannot be said for mapping the as-is state. There the opinions tend to diverge quite dramatically – almost in a binary way – into one of two camps: ‘Believers’ […]
10 Steps to Turning Your Mediocre ERP Implementation into GoldÂ
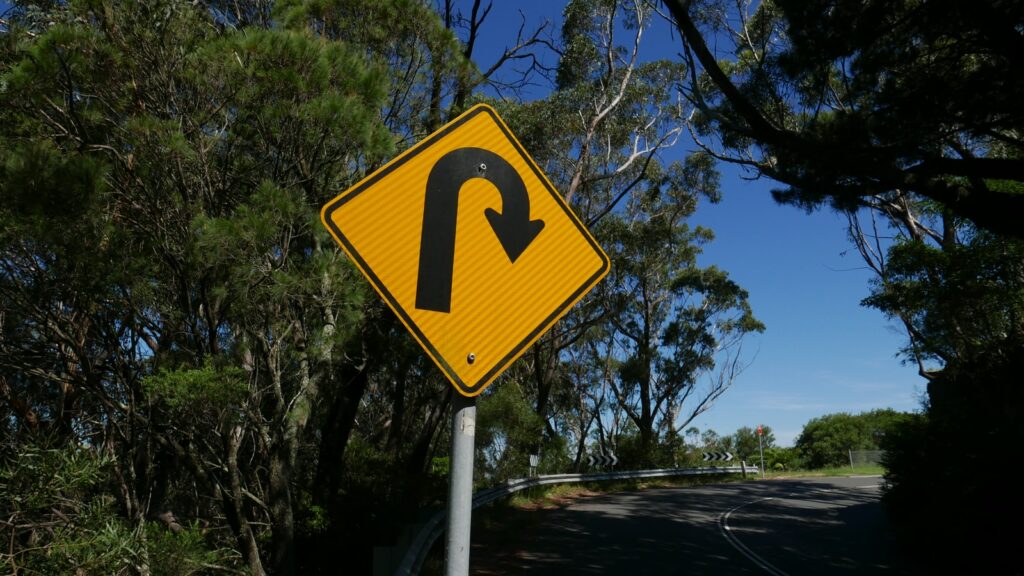
Thousands of companies every year spend millions of dollars chasing the ERP dream, only to come up short. But it’s not too late to turn things around. That promised land still lies ahead, and the waters you must navigate to get there may not be as murky as you think.
Top 5 ERP Pain Points
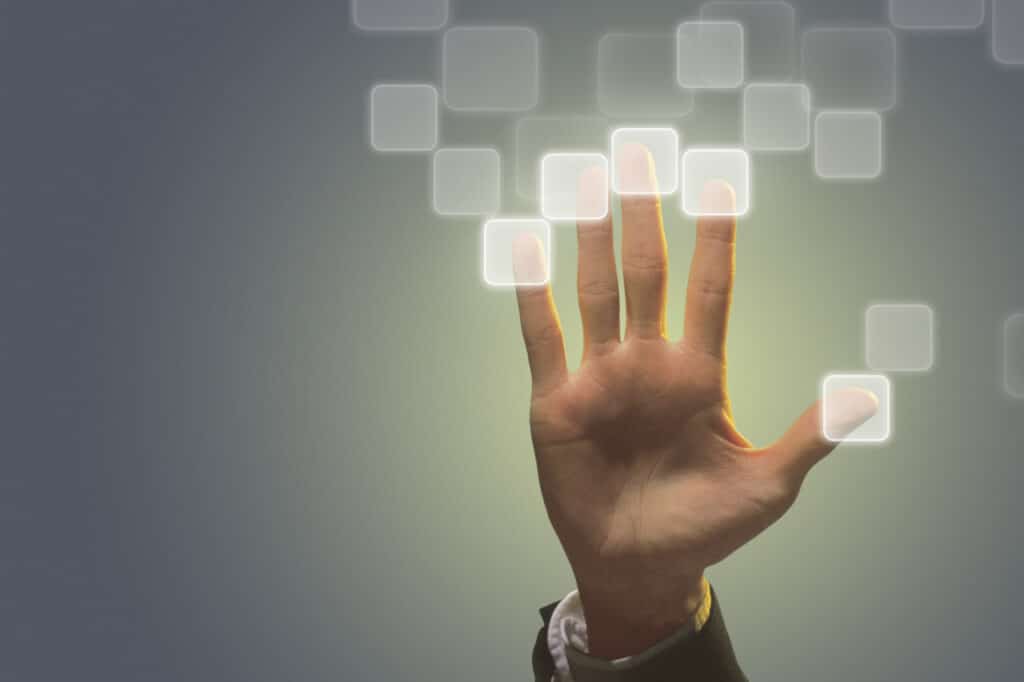
One of the most important business systems that almost every company has is an Enterprise Resource Planning (ERP) system. These are hugely complex software programs that handle everything from employee management to inventory and customer relations, all in real-time. In short, they’re some of the most critical components for a successful business. With that said, […]